The Case For In-House Manufacturing Of Cell Therapies

By Erin Harris, Editor-In-Chief, Cell & Gene
Follow Me On Twitter @ErinHarris_1
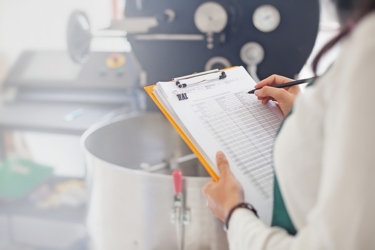
Many therapeutic developers in the cell therapy space have turned to professional manufacturing organizations, both CMOs and CDMOs, to help develop and manage their manufacturing programs. This option especially makes sense for small developers that do not have the resources to build — or even consider — in-house manufacturing for their therapies. As such, for some developers, outsourcing is the most efficient option. But partnering with CMOS and CDMOs does not always make the most cost-effective sense especially when speed to clinical trial is most important. In fact, according to ARM, when outsourcing, “the developer may have less oversight over the manufacturing process, and disruptions at the CMO or CDMO can create bottlenecks for the developer, particularly if they rely on a single CMO or CDMO to fulfill their needs. In addition, most current generation regenerative medicine products are highly specialized, requiring bespoke components and specifically trained staff. The traditional CMO model struggles to accommodate such unique and non-standard technology approaches, which can result in delayed tech transfer and negatively impact the developer and their patient population.”
As such, the speed with which developers must provide therapies through a complicated manufacturing process is a critical reason to bring manufacturing in-house, especially if developers do not have a solid relationship with a trusted CMO or CDMO partner. Further, there are several therapy developers that state having control over at least part of the manufacturing process provides an advantage not only from a quality control perspective but also provides the flexibility to move quickly to address changes in procedure that inevitably arise. In-house manufacturing provides control over whom you recruit to manufacture the therapies. And, there are plenty of SMEs who suggest that having in-house manufacturing is something every developer should strive for even when continuing to rely on a CMO or CDMO for certain aspects of the manufacturing process such as planning for more capacity.
Adaptimmune, for example, is a fully integrated cell therapy company with in-house manufacturing as well as vector production capabilities. This full integration has enabled rapid process improvements as well as the ability to streamline various steps to ensure a shorter manufacturing time. Yet, GMP manufacturing puts providers, patients, and payers are at risk for failed manufacturing processes given the stringent demands of compliance and regulatory approval. Build a team with rock solid understanding of GMP and cGMP manufacturing. QA and QC support is essential, and if budgets and resources do not allow you to hire your own team, consultants are a viable option. Use automation platforms, such as a comprehensive cell therapy automation platform, whenever possible to alleviate the issues associated with the manual documentation process.
From an autologous therapy perspective, some SMEs state that bringing manufacturing in house is the only path forward given the dynamic, ever-evolving nature of the technology. However, if you have a long lead time, your speed to clinical trial is not as concerning, and/or you’re able to wait for capacity to become available, partnering with a CDMO is the option worth exploring.