Reducing Product Loss With Process-Independent Biomanufacturing
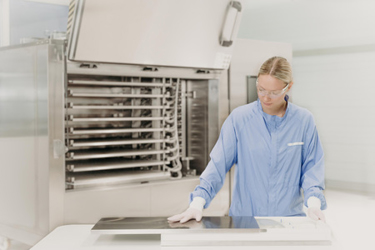
The lack of prior infrastructure as well as process constraints required process flows that were conceptually thought through from scratch. It opened doors to optimize fluid handling functionalities that fostered operational and cost benefits in the long term. With having different single-use technologies in place, though, the CDMO had already planned to implement existing spare platform systems for their new facilities.
With the resulting balancing act between saving costs and achieving a process-efficient manufacturing setup, the company needed to find a way to limit the total cost of ownership, consisting of capital expenditures (CAPEX) upfront and operational ex- penditures (OPEX), while at the same time improving their biopharmaceutical fluid management’s overall performance and minimizing product loss.
With the implementation of RoSS® shells, a multinational CDMO has been able to standardize its fluid management process thanks to the protective shell’s bag-independence, and regardless of size and type of single-use bag used.
Read how modular and vendor-agnostic end-to-end process solutions help save CAPEX, while increased process speed at different scales help reduce OPEX.
Get unlimited access to:
Enter your credentials below to log in. Not yet a member of Cell & Gene? Subscribe today.