Inside the Planning of Audentes' Future Manufacturing Facility

By Erin Harris, Editor-In-Chief, Cell & Gene
Follow Me On Twitter @ErinHarris_1
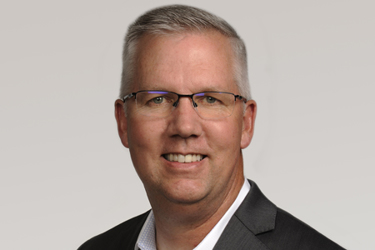
Audentes’ Sanford, NC future facility, which will manufacture the company’s portfolio of adeno-associated virus-based gene therapies aimed at targeting serious rare neuromuscular diseases, is slated to be operational next year. Donald Wuchterl, Audentes’ Senior Vice President, Technical Operations talked to me about the best practices he and his team have implemented thus far in the planning stages, equipment needs, challenges and solutions, and more.
Audentes’ Sanford, NC future facility, which will manufacture the company’s portfolio of adeno-associated virus-based gene therapies aimed at targeting serious rare neuromuscular diseases, is slated to be operational next year. What are the best practices you and your team have implemented thus far in the planning stages for the manufacturing facility?
Wuchterl: During the base building selection and design phases of the project, we focused on creating an expandable facility that can rapidly grow with and meet the needs of the Audentes / Astellas AAV product portfolio well into the future. From an execution standpoint, the site is planned as a multi-phased modular expansion that will add additional production suites without impacting the ongoing operations of previously built-out and licensed phases.
To manage budget, we negotiated a guaranteed maximum price and a shared savings agreement with the general contractor (GC). This shared agreement helps to lock in the project budget and incentivizes the GC to find savings along the way. This is a true win-win for the GC and the owner.
We have also sought ways to integrate local offerings and create mutually beneficial alliances in the area, one of which is with Duke Energy One. Duke Energy One is providing a comprehensive base and emergency power solution for the site including maintenance and operation services. This strategic relationship allows us to take advantage of Duke Energy One’s depth of knowledge and experience in the electrical field while freeing capital funds to redirect to other parts of the project.
Do not underestimate the importance of onboarding key site leadership early on in the project. We have already hired our site head and several leadership and functional roles for facilities, engineering, manufacturing, validation, and quality. This is about 12-18 months ahead of our cGMP start. This site core team will be responsible for taking the facility from construction handoff through commissioning and validation. Additionally, these leaders will be responsible for any remaining operational readiness activities including: hiring, training, and onboarding the remaining team, policy and procedure generation and approval, validation execution and oversight, process tech transfer, shakedown and engineering batches, and eventual escalation to full cGMP operations.
What challenges have you encountered, and how are you handling them?
Wuchterl: Of course, no one anticipated building out the facility in the middle of a pandemic. Our typical project team working dynamic has shifted to more remote work with tools like Zoom, Box, and MS Teams. We are pleased that we recently installed trailers at the site for our Audentes employees and contractors. So, we are slowly transitioning to the job site / office dynamic we were used to pre-pandemic, albeit under strict protocols ensure we are protecting everyone’s health.
As with any large capital project there are unforeseen site, design, and/or procurement issues that arise. To date these have all been very manageable, but the project is still in an early phase and has about another year of construction, so new issues may arise. When these happen, the best approach is strong collaboration with the architectural & engineering firm, general contractor, and / or equipment vendor to work together on solutions. The end goal is to provide a state-of-the-art facility producing high-quality gene therapies that are critical for the patients and families in need. The cross-functional team we have built, including all key vendors and contracted services working on the project all share this mission.
Is there anything you would do differently out of the gate, and if so, please explain.
Wuchterl: Although this has not impacted us significantly, I believe that we might have done a better job estimating the appropriate project contingency. A healthy contingency helps speed things up when unexpected issues arise. Without it you have to navigate the financial processes for unbudgeted scope, and that can have implications on the overall project timeline. It is always a trade-off. Determining the appropriate project contingency early on is challenging, especially when the project budget is established ahead of final drawing sets or contractor / subcontractor bid estimates.
From an equipment perspective, what challenges has Audentes faced that the company was not anticipating, and how did it overcome them?
Wuchterl: We have not had any significant equipment issues so far. I think this is because we have spent the last five years fine-tuning our process at our existing South San Francisco cGMP manufacturing facility. So, we made the decision early in the project planning that we would take most of our platform process (including equipment type and vendor) and duplicate it at our Sanford site, the only difference being a slight increase in scale.
What manufacturing equipment is essential for the company to scale?
Wuchterl: Our new Sanford manufacturing facility is designed to be built out over three phases. In the initial phase of the build out, we are adding manufacturing suites to support 4000L of bioreactor capacity (two production trains each with 2x1000L single use production scale bioreactors). To put this in perspective, our South San Francisco facility operates one 2x500L bioreactor train. We have designed the Sanford facility to support significant growth in future phases. Current design can support even larger scale bioreactors. So as demand grows, we can expand this facility to 20 times our current South San Francisco capacity.
What other information can you offer regarding best practices in equipment selection?
Wuchterl: Taking the time to properly develop user requirement documents ahead of the vendor bid process is crucial to ensuring you get what you need. All this documentation can slow things down, but a well-run project will take the time to do this. Later, these documents will serve as the basis for the validation activities. Do not underestimate the workload with these and other foundation documents. Even though we were leaning towards our current platform vendors, we still went out to bid from multiple competing vendors. This was not only a way to help drive costs down, but also to stay up to date on the current vendor offerings. There are a few examples where we deviated from our South San Francisco equipment list and went with another option because there were newer versions or additional offerings that were not available when procuring equipment for the original South San Francisco facility.