Expression Therapeutics' In-House Manufacturing Model — How And Why

By Erin Harris, Editor-In-Chief, Cell & Gene
Follow Me On Twitter @ErinHarris_1
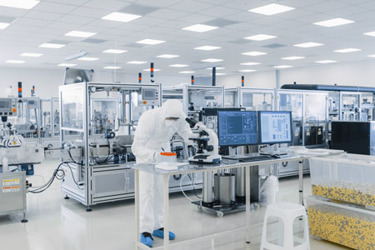
Just recently, Expression Therapeutics announced the appointment of Bill Swaney as its Vice President of Manufacturing. The company’s press release addressed that under Swaney’s leadership, the manufacturing team has not only its own therapeutic pipeline but also in-house manufacturing with its upcoming 43,000 square foot manufacturing facility in Cincinnati, OH. “The facility will manufacture lentiviral (LV), retroviral (RV), and adeno associated viral (AAV) GMP vectors, with a mix of 30-180 liter runs in cell stacks and up to 1,000 liter runs in bioreactors, and will have the capability to manufacture up to 100 GMP vector products per year. Additionally, it provides the necessary infrastructure to fulfill Expression Therapeutics' ex vivo cell processing and recombinant protein production needs. Expression Therapeutics is using prefabricated PODs from G-CON Manufacturing, Inc. for its ISO Class 7 cleanroom suites.”
I caught up with Swaney for his input on why Expression Therapeutics is building its own clean room and the benefits of doing so.
What They’re Saying
According to Swaney, Expression Therapeutics has a rich therapeutic pipeline of advanced therapeutic medicinal products (ATMPs) for hemophilia, neuroblastoma, T-cell leukemia/lymphoma, acute myeloid leukemia (AML), and primary immunodeficiencies such as hemophagocytic lymphohistiocytosis (HLH).
“Our lead candidate, CD68-ET3-LV, a lentiviral vector for the treatment of hemophilia A, has been manufactured, certified, and a Phase 1 Study has been approved by the FDA,” says Swaney. Recent clinical successes with concomitant regulatory approval of several prominent ATMPs have resulted in hundreds of new ATMPs entering product development, most with aggressive timelines for clinical trial initiation. This surge has strained all areas of ATMP manufacturing.
Why It Matters
Swaney explains that with viral vectors being a major rate limiting step for ATMP manufacture, it is not surprising that vector manufacturing needs have outpaced existing viral vector manufacturing capacity. Wait times for viral vector manufacturing slots can exceed 18 months and, when combined with the duration of manufacturing and subsequent 4-5 months required to complete safety and release testing on the manufactured vector, as well as the manufacture and testing of the cellular product itself, the time to open the trial can easily exceed two years. This duration was one of the primary drivers that led Expression Therapeutics to conclude that building out its own manufacturing facility would be ideal.
The facility design is comprehensive with adequate laboratory space, an independent cell processing area, early phase GMP vector manufacturing area consisting of modular cleanrooms, and a separate area for support of commercial manufacture for both their viral vector and protein products. “We see several direct benefits to having our own in-house manufacturing capabilities,” says Swaney. “The primary benefit is having direct control over our viral vector and cell manufacturing. Additionally, we have maximal flexibility to change manufacturing schedules as product development or demand changes.”