IPS-Integrated Project Services
Sales
721 Arbor Way, Suite 100Blue Bell, PA 19422 US
610.828.4090
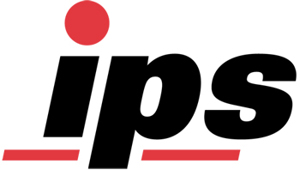
Company Overview
IPS-Integrated Project Services is a global provider of technical consulting, architecture, engineering, project controls, construction management, and CGMP compliance services for technically complex pharmaceutical development and manufacturing facilities worldwide.