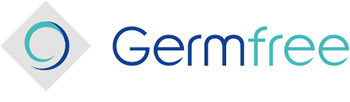
ABOUT GERMFREE
Germfree manufactures a comprehensive line of barrier systems for aseptic control and containment as well as a complete mobile and modular cGMP facilities. We offer advanced solutions to maintain cGMP processes and production for a wide range of biopharmaceutical applications. We are a single source OEM provider of complete cleanroom and lab facilities, and the corresponding integrated equipment designed an purpose-built by our leading-edge fabrication technology, engineering teams and subject-matter experts.
FEATURED PRODUCTS
ARCOPLAST CLEANROOM COMPONENTS
ARCOPLAST CLEANROOM WALL AND CEILING PANELS
VIDEOS AND WEBINARS
CONTACT INFORMATION
Germfree
4 Sunshine Blvd
Ormond Beach, FL 32174
UNITED STATES
Phone: (386) 265-4360
NEWS
- Germfree Launches Smarthood™: A Groundbreaking, Software-Agnostic IV Workflow Solution Transforming Sterile Compounding
- Germfree Acquires Cleanroom Wall And Ceiling OEM Arcoplast
- BioIVT Opens Facility With New Cleanroom From Germfree In Winchester VA
- Germfree Announces The Appointment Of Four Independent Board Members
- Germfree and Orgenesis Announce Asset Purchase And Strategic Partnership Intended To Revolutionize Cell And Gene Therapy Through Decentralized Production And Global Accessibility
- Germfree Laboratories And Title21 Health Solutions Transform Cell And Gene Therapy Manufacturing With Decentralized Innovation
- Novel Mobile Cleanroom Technology For Advanced Therapies
FEATURED ARTICLES
-
Navigating the inherent conflicts between GMP and biocontainment regulations is critical when designing specialized cleanrooms for advanced therapy manufacturing.
-
Learn about a collaboration that has yielded advanced modular cleanrooms, integrating cutting-edge building automation, critical monitoring, and data aggregation for manufacturing intelligence.
-
Gain insight into the mobile cleanroom that was created to accommodate the needs of Moffitt Cancer Center's Oncology Infusion Pharmacy Services and adhere to USP <797> and <800> standards.
-
Learn about the modular BSL-2LS cGMP facility that was constructed to support 3 processing lines for German-based CDMO Vibalogics as the company sought to expand in the U.S. market for viral vectors.
-
Learn about the USP 797 and 800 compliant drug compounding pharmacy cleanroom trailer that was supplied to Duke Raleigh Hospital during renovations of its main building to support the heavy workload.
-
Learn about the cutting-edge mobile BSL-3 laboratory that was custom-built in response to a need for a flexible diagnostic testing solution in the United Arab Emirates due to a surge in COVID-19 cases.
-
Uncover how Germfree designed and installed a mobile cGMP cleanroom on a 53′ tractor-trailer chassis to provide a flexible and efficient cleanroom solution tailored to the company’s needs.
-
The delivery of this mobile cGMP cleanroom facility to ACT showcases Germfree’s commitment to providing innovative solutions that meet clients' unique needs and contribute to advancing healthcare.
-
Discover NIH's innovative solution to clinical-stage viral vector production: See how two mobile cGMP facilities deliver adaptability and compliance to Bethesda's National Institute of Health.
-
Discover how Germfree Laboratories overcame challenges for the Royal Canadian Mounted Police by designing a mobile lab with advanced biocontainment and state-of-the-art communication systems.
-
This project showcases Germfree’s capacity to provide cutting-edge, bespoke solutions in pharmaceutical manufacturing, underpinning their dedication to innovation, safety, and quality.
-
Completed in 2021, learn how this custom BSL-3 mobile laboratory received PHAC approval and ensured a secure environment for PPD powder-related MTech development work.
-
Discover how Germfree tackled a unique challenge from the Public Health Agency of Canada by designing a custom Class III biosafety cabinet for advanced virology studies and disease surveillance.
-
Uncover how AST's satisfaction with Germfree's solution led to the acquisition of two additional units, showcasing the project's success and Germfree's expertise in tailored cleanroom solutions.
-
Explore how clinical testing was transformed with a pioneering BSL-2 mobile laboratory on a Sprinter Van platform to enhance safety and portability for advanced biosafety requirements.
-
Discover how this mobile lab enhances rapid outbreak response and safely manages highly infectious pathogens, showcasing Germfree's expertise in biocontainment solutions for critical health crises.
-
Learn how Germfree's 53-foot mobile cleanroom trailer ensured uninterrupted sterile drug compounding during a facility renovation.
-
Explore the development of a mobile Biosafety Level 2+ (BSL-2+) facility adhering to cGMP for early-phase clinical trial manufacturing.
-
This custom-designed, eight-foot isolator helped a client meet their decontamination needs, maintaining ISO-5 sterile conditions while decreasing turn-around time for filling small batches.
-
The client required a freestanding COVID-19 research facility on an accelerated timeline built for continuous use in the cold climate of the northeast United States without a shell building.