What You Need To Know About Cold Chain Durability Of Fluoropolymer Bags
By Joe Cintavey and Meghan Meeuwissen, Gore PharmBIO Products
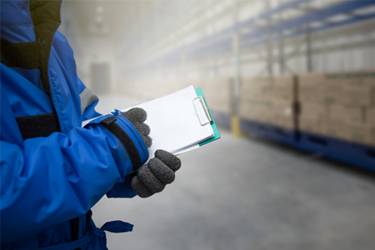
Biologics such as vaccines, cell and gene therapies, tissues, and recombinant therapeutic proteins now make up more than a third of all pharmaceutical sales in the U.S.1 Because these valuable drug products are isolated from or can themselves be living organisms, they are typically frozen and stored at temperatures between -40°C to -80°C to remain stable.
As the biologics market continues to grow, drug manufacturers are looking for packaging solutions that maintain integrity during processing and freezing, are easy to scale up to larger volumes, and remain robust throughout the temperature-controlled supply chain. However, finding the right containment system requires more than looking over a spec sheet. Here are some important considerations to keep in mind when choosing packaging for a biologic drug substance.
Why are bags better than many other container choices?
When storing and transporting biologics, the type of container is an important consideration. Biopharmaceutical manufacturers are increasingly choosing single-use bags with aseptic connectors to store bulk drug product throughout the cold chain. One of the most important advantages of bags is that they allow for a closed system that minimizes the risk of contamination. Steel canisters, glass vials, and bottles typically require under-hood processing which increases the risk of the product being exposed to the environment, which brings a risk for contamination. Bags with aseptic connectors, however, contain the biologic product within a closed system throughout processing, even during the freezing process. When other containers such as bottles are frozen, the different materials used to make the screw top and bottle could expand and contract at different rates, compromising the integrity.
An additional benefit of bags is that they are easier to work with when scaling up from the smaller volumes manufactured during the development stages to full-scale drug production. Ideally, biopharmaceutical manufacturers like to simulate high-volume production during the clinical stages. This can be problematic with some containers because the surface area to volume ratio for a 10-milliliter vial is much different than a one-liter bottle, for example. This can not only cause issues with predicting the stability of the biologic interacting with the container material but can also affect the freezing process because the distance between the container surface and its center will be different.
Bags, on the other hand, feature a surface area-to-volume ratio that remains more consistent as processes and product volumes scale up from small (50 ml bags) to larger (5 to 12 liter) bags. This allows better prediction of how freezing and interactions with the bag material will impact the stability of the bulk drug substance when moving to the manufacturing stage.
What is the glass transition temperature and why is it not specific enough to indicate cold chain performance?
Single-use bags have many advantages but are often made from materials that become brittle and will crack when handled at temperatures from -40°C to -80°C. This can lead to loss of a high-value biologic product. For cold chain storage, bags made of fluoropolymers are a great option because they remain durable and flexible over a wide temperature range. However, it is important to realize that not all fluoropolymers are the same. Even fluoropolymers with a similar wide temperature range can vary greatly in cold durability performance.
One characteristic often referred to when choosing cold chain storage containment systems is the glass transition temperature, the temperature at which a polymer turns from ductile to hard and brittle. But be aware that although glass transition temperature is the most cited — and sometimes only — material property used to explain material performance in cold chain applications, it does not provide a complete picture of performance for a specific application. The glass transition temperature is a good starting point for narrowing down appropriate materials for cold chain applications, but it is critical to look beyond this property to figure out how a specific fluoropolymer will actually perform in a filled bag at very cold temperatures.
What types of testing and analysis can provide guidance in evaluating cold chain durability?
Although the glass transition temperature may indicate that a material is rated for use at a certain temperature range, a bag made of this material may not hold up to the rigors of handling or being dropped at these temperatures. Only performance testing and film-level analysis can provide this information. It is important to look for bags that have been tested for durability through a wide range of cold chain testing, such as multiple freezing and thawing cycles. Frozen impact testing can also show how the packaging will respond to a direct impact like being dropped. Other tests are used to simulate conditions during shipping, where vibrations cause friction that could lead to a failure through mechanisms that are much different from a direct impact.
In addition, we also use a special film flex test to aggressively flex and twist our fluoropolymer film to simulate conditions that might be experienced during frozen handling and transport of the bags. This is all performed at -80°C, the typical low end of the temperatures used for many cold chain applications.
What else do I need to keep in mind when selecting packaging that will perform well at low temperatures?
When selecting packaging for your valuable drug product, it’s important to partner with a packaging manufacturer that has both materials engineering knowledge and experience with cold chain applications. Gore meets these needs with a thorough understanding of how single-use materials can be affected by handling in the cold chain. Our experts know how to manipulate the structure of the fluoropolymer polytetrafluoroethylene (PTFE) to maximize durability at cold temperatures.
Drawing on this extensive expertise and experience, we developed the GORE® STA-PURE® Flexible Freeze Container bag for storing and transporting bulk drug substances. By combining PTFE with a patented bag design, these containers are made to withstand frozen handling and maintain integrity after rigorous testing.
We tested these containers by filling them with a phosphate-buffered saline solution and freezing them in both blast and plate freezers until completely frozen. Filled and frozen containers maintained integrity after each of the 3 following independent tests: being dropped from 3 feet onto a concrete floor, five cycles of freezing and thawing and 12 months of frozen storage. These tests help assure biopharmaceutical manufacturers that these advanced containment systems will reduce the risk of product loss during cold chain processing, storage, and transportation. Partnering with Gore provides access to a team of experts with years of materials science and experience in improving the processing and delivery of pharmaceutical products.
To learn more, visit https://www.gore.com/products/gore-sta-pure-flexible-freeze-container.
About Gore
W. L. Gore & Associates is a global materials science company dedicated to transforming industries and improving lives. Since 1958, Gore has solved complex technical challenges in demanding environments — from outer space to the world’s highest peaks to the inner workings of the human body. For the pharmaceutical and biopharmaceutical industry, Gore is helping those in drug discovery and manufacturing compete in this increasingly regulated landscape with reliable solutions for purifying, transferring, storing, filtering, processing, and packaging. These solutions include durable, multi-use process components and single-use products that enable researchers and manufacturers to control costs through process improvements.
Reference