Top 5 Mistakes To Avoid When Measuring Overall Equipment Effectiveness (OEE) In Pharma Packaging
By Valerio De Simone, Ph.D., Adept Packaging
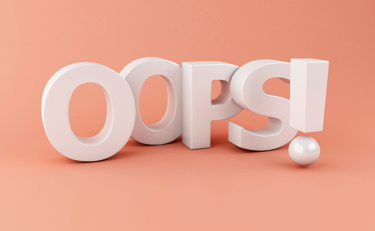
Although compliance has been the buzzword in the pharmaceutical industry for decades, recently the industry’s focus has been shifting toward efficiency. Every new packaging machine is equipped with digital technology, and their data can typically be used to increase the visibility of the operations. The upcoming post-COVID-19 financial crunch will certainly reinforce and accelerate efforts to increase efficiency by streamlining costs and, at the same time, increase throughput. Despite its (apparently) trivial formulation, overall equipment effectiveness (OEE) is one of the most misleading key performance indicators (KPIs) ever used in the manufacturing world. This article will examine five of the most common mistakes companies will want to avoid when dealing with OEE.
1. The world is analog: Automated systems don’t tell the whole story.
Demand for OEE tracking systems is exploding, as they are seen as the panacea for discovering losses on running packaging lines. Although they can undoubtedly provide valuable information, these sensors and algorithms have only limited visibility on actual packaging operations. Automated lines are often considered as systems with predictable performance, but human activities can significantly change them. For example, an operator busy with a leak test could neglect a jam that happened on a machine, resulting in a longer line stoppage. On the other hand, an experienced supervisor can adjust the machines to their best and resolve issues efficiently, thus considerably cutting down the rejection rate. Live OEE dashboards generate the “wow” effect, which helps boost sales but provides very limited benefits to equipment performance in the long term. Without proper contextualization, data from OEE tracking systems are unable to provide a complete picture and can even sometimes be misleading by shifting the focus only to the automation issues.
2. Think outside the box: Losses can come from outside of the packaging line.
We mentioned that losses can be outside of the detection range of digital sensors installed at the packaging line level. Surprisingly, they are often far from the packaging line itself. Reasons for rejects, slowdowns, and stoppages could reside in superordinate IT systems and interfaces, consumables suppliers, or other company departments. For example, even the best changeover procedure cannot cope with excessive variability in the packaging dimensions or, similarly, missing batch documentation due to inefficiencies in the scheduling office could jeopardize the batch start. It is fundamental to have a holistic approach to efficiency, striving to find the root causes for the losses seen at the packaging level, even if this requires a long journey from where they appeared. The only effective way to achieve this goal is through the development of a lean manufacturing culture within the company.
3. Garbage in, garbage out: Measure what matters
What can be easily measured, maybe because it is already monitored by a sensor with historical data at hand, is rarely a good proxy for what is required for an assessment capable of providing valuable information to improve the line effectiveness. Inputs for OEE calculation often come from the newest machines, which might not be the line bottleneck. For example, measuring the rejection rate of a machine that can reprocess its rejects without slowing down the throughput of the line has no real value and is rather misleading, because its rejects are not affecting the line quality rate. Only the cause of the line bottleneck reduces the performance of the line, but this is often an old machine without adequate sensors. Unfortunately, instead of installing additional sensors, the system suppliers often opt for collecting inputs already available from the newer machines. A shining OEE dashboard that does not require any manual activity or line revamping projects is a temptation for any packaging manager. However, taking decisions based on wrong information is a tangible risk because the business intelligence tool elaborates on the wrong inputs.
4. All that glitter is not gold: Be careful with benchmarks.
A higher OEE is typically desirable, but this might not be always the case. In particular, there is one loss that could be the result of a wise business decision: the setup time. Small batches let the business cope with a variable demand by reducing the lead time and releasing capital from warehouse stockpiling but, inevitably, diminishing the OEE. In fact, frequent product changes imply more time spent on nonproductive activities such as component changeovers, product-specific adjustments, batch start activities, and batch closure activities. Each company adopts a different production strategy, and different production lines could have completely different performance levels depending on their production mix (e.g., dedicated to a single product vs. a wide variety of formats and materials). As a result, comparative analyses are more meaningful when performed between lines running similar products (e.g., twin lines) or, if possible, on the same line before and after a change in the process or in the technology.
5. Historical data does not account for disruptive events.
Engineers are used to basing their analyses on historical data. History is a great teacher, but it cannot be used to foresee uncommon disruptive events that might not have happened in the past. The best way to proceed is by performing a process failure mode and effects analysis (P-FMEA) of the entire packaging process, starting from the scheduling and considering all IT and automation systems/interfaces, the packaging activities (automated and manual), and eventually the batch closure activities. Wherever possible, risk and criticality should be assessed from historical data and/or analytical analyses. This might not be possible for exceptional failure modes for which expert surveys could be the only alternative. Nevertheless, it is essential that the analysis is not limited to what is well known and easy to assess, because these last events are often disruptive and sometimes can be strongly mitigated with very simple preventive actions.
Conclusion
New automation and IT technologies are deeply changing the manufacturing industry, offering new ways to track performance and improve operational efficiency. Nonetheless, it is more important than ever to remember that these are only tools that should never be used to guide decisions without a proper preliminary analysis.
About The Author:
Valerio De Simone is a manager at Adept Packaging, which provides packaging consultancy services ranging from packaging development management to track and trace implementation. He spent the last five years serving the pharmaceutical industry for several internal projects, all related to the packaging area. His main fields of expertise are serialization and track & trace, business process analysis and optimization, lean manufacturing, and OEE. He holds a Ph.D. in Operations Management from Tor Vergata University of Rome. If you have questions or would like to learn more about OEE, contact De Simone at valerio.desimone@adeptpackaging.com.