New ISO 14644-21:2023 Addresses Reducing Sampling Errors With Airborne Particle Counters
By Tim Sandle, Ph.D.
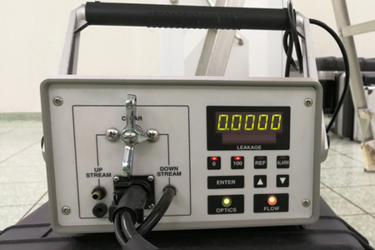
Particle counting in cleanrooms is performed using a variety of optical particle counters (aerosols passed through a focused light source, where the scattered light is converted into electrical pulses which allow the counting of particles).1 These are designed to detect the number of particles of a given size from a given volume of air.2 The higher the cleanroom class (such as EU GMP Grade A/ISO 14644 class 5), the greater the impact the factors that affect the accuracy of particle counting become.
It is the topic of optimizing particle counter accuracy that the latest part of the ISO 14644 cleanroom standards addresses. Part 21 of the standard was released during August 2023.3 The standard takes the form of a technical report, focusing on reducing sampling error and particle loss. The new addition is formally linked to ISO 14644 parts 14 and 25 (in turn, these parts form part of EU and PIC/S GMP in terms of Annex 16 and the FDA’s aseptic processing guidance).7
Use Of Airborne Particle Counters
The particle counters covered in the standard are airborne counters, commonly used to classify cleanrooms in pharmaceutical and healthcare manufacturing and for ongoing monitoring of controlled environments. Such counters are more formally referred to as light scattering airborne particle counters (LSAPCs) and the recommended standard for their design and calibration is ISO 21501 (in particular, Part 4:2007).8 Particle counters, calibrated to ISO 21501, pass the assessment if they record a counting efficiency of ±50% or better based on the smallest size measured as part of the calibration exercise (with the particle size at 1.5 times the smallest size having a counting accuracy of ±20%). Most particle counters will give occasional false readings, particularly for the ≥5.0 µm particle count, due to electronic noise, stray light, or a sudden release of particles.
For the classification of cleanrooms in pharmaceutical facilities, particle cutoff sizes of ≥0.5 µm are typically examined. For ongoing assessments and for batch-related monitoring activities, EU and PIC/S GMP require an additional cutoff particle size to be examined: ≥5.0 µm (these sizes refer to the diameter of the particle). This particle size is perhaps more representative of microbial carrying particles, the majority of which will be formed of skin detritus.9 This particle size is typically not used for cleanroom classification because of the limit applied and the sample size that would be required relative to the possibility of particle loss. It is, however, a strict requirement for assessing larger size particles to understand activity-based operations, especially aseptic processing.
All particle counters have a degree of inaccuracy in terms of counting, in that not every particle that is passed into the instrument is counted through the light scattering process and detectors. In addition, not every particle that is drawn in as part of the initial sample reaches the laser, primarily due to the phenomenon of “drop-out” as particles are carried in the sampled air path and are directed toward the counter optics. There are a number of operational factors that can improve counting accuracy and minimize particle drop-out.
Tubing
Particle counters can be operated with and without tubing. The general recommendation, as set out in the standard, is to avoid tubing where possible. Each time tubing is used there is a loss of particles, and the longer the tubing is, the greater the particle loss. However, the degree of loss is not simply a factor of the tubing length as the straightness of the tubing relative to any kinks affects the likelihood of particles adhering to the inner surfaces of the tubing. The tubing material matters as well, with some materials having an electrostatic charge that can pull particles from the airstream. The flow of air through the tubing and toward the counter is also a determinant.
Tubing is unavoidable when you need to situate counters outside of unidirectional airflow devices (to avoid particulate generation from counter exhausts). In these circumstances, the tubing should be as short as possible. However, unlike the “absolute” value quoted in Annex 1 (at less than 1 meter), the standard acknowledges the complexities of fitting tubing in RABS and isolators for fixed counters. It recommends that a particle loss assessment be conducted. Bore size and the particle counter flow rate are required to make such an assessment and understand the tubing. Tubing length is defined as that between the sampling head probe and the particle counter.
Hence, tubing of 2 meters could be justified for fixed particle counters in a RABS provided the number of bends does not exceed three. Importantly, the number of bends correlates with particle loss. For example, as the standard indicates, ≥5.0 µm particle size losses reach 20% at 2 meters where 10 mm diameter tubing is used. With tubing bends, the larger the radius, the better, with a minimum of 15 cm being the starting point. However, a bend in itself will have different risks of particle loss depending on the flow rate and diameter. Tubing of a diameter of 10 mm to 15 mm also ensures that the tubing has the correct Reynolds number (the ratio of inertial (resistant to change or motion) forces to viscous (heavy and gluey) forces; the objective is to achieve a Reynolds number of >2,200 to ensure effective turbulent flow along the tubing).
Another factor that can influence particle loss is the material of construction for the tubing. For tubing materials, stainless steel is preferred (although it is inflexible and this limits its application), followed by Bev-A-Line, with Tygon suitable for higher temperatures. These materials are designed to prevent charged particles from adhering to the tubing surface. Bev-A-Line or Tygon tubing are types of co-extruded tubing consisting of a PVC exterior and a thermoplastic polyester elastomer interior. The suitability of such material for particle counter tubing relates to the relative smoothness of the interior wall.
In addition to what is conveyed in the standard, all particle counter tubing will, over time, accumulate particles, particularly where particle counters are used for continuous monitoring. This means tubing should be replaced regularly.
Positioning Of Particle Counters
The standard considers the location of particle counters, indicating they should be situated lower than the sample height to avoid sampling upward through tubing. This helps to avoid further particle loss. With Grade A/Class 5 unidirectional airflow, particle counting should normally be conducted at the working height. This position will vary according to different activities (the location of particle sources within the room and equipment and personnel may influence the transport of particles). As a rule of thumb, this is should be no greater than 30 centimeters from the activity to be sampled. Airflow velocity readings or airflow visualization data can help to guide the optimal probe location.
Isokinetic Probes
For sampling Grade A/Class 5 environments and under any unidirectional airflow device, an isokinetic probe is always fitted to particle counter tubing. The purpose of an isokinetic probe is to ensure that the velocity of the air going into the sampling probe nozzle is equal to the velocity of the undisturbed air at that point. Through this, the air entering the counter is disturbed as little as possible so that the same particles go into the probe as would have passed the area of the probe had it not been there. This ensures that a more accurate count is obtained. The probe of a particle counter must always be oriented in the direction of the airflow, e.g., for a vertical unidirectional airflow device, the probe must be oriented upward; for a horizontal unidirectional airflow, the probe must be oriented sideways in the direction of the airflow; and in a turbulent flow room, the probe must be oriented upward.
The correct isokinetic probe must be fitted to the appropriate counter because counters with different flow rates require different sizes of isokinetic probes, e.g., 28 l/m vs. 50 l/m and in relation to different air velocities. The acceptable particle loss (sampling error) from the use of an isokinetic probe is up to 5%. Guidance is provided in the standard for isokinetic probe orientation, as expressed as the number of degrees permitted (target of 0 degrees and no greater than 20 degrees).
Each of the measures recommended in the standard can be adopted to optimize the recovery of airborne particles using optical particle counters as part of the contamination control program.
References
- Sandle, T. Clean room design principles. In Esteves, S., Varghese, A. and Worrilow, C. (Eds.) Clean Room Technology in ART Clinics: A Practical Guide, CRC Press, pp76-90
- Akey, J. (2005) Info Overload: What Do My Particle Counts Mean?, Indoor Environment Connections, 6 (11): https://cleanroom-solutions.astechireland.ie/sites/default/files/2020-10/__What_do_Particle_Counters_Mean.pdf
- ISO/TR 14644-21:2023 Cleanrooms and associated controlled environments — Part 21: Airborne particle sampling techniques, ISO, Geneva
- ISO 14644-1:2015 Cleanrooms and associated controlled environments — Part 1: Classification of air cleanliness by particle concentration, ISO, Geneva
- ISO 14644-2:2015 Cleanrooms and associated controlled environments — Part 2: Monitoring to provide evidence of cleanroom performance related to air cleanliness by particle concentration, ISO, Geneva
- The Rules Governing Medicinal Products in the European Union, Volume 4 EU Guidelines for Good Manufacturing Practice for Medicinal Products for Human and Veterinary Use, Annex 1, Manufacture of Sterile Medicinal Product, European Commission: https://health.ec.europa.eu/system/files/2022-08/20220825_gmp-an1_en_0.pdf
- Sterile Drug Products Produced by Aseptic Processing — Current Good Manufacturing Practice Guidance for Industry, FDA-2003-D-0145: https://www.fda.gov/media/71026/download
- ISO 21501-4:2007 Determination of particle size distribution — Single particle light interaction methods — Part 4: Light scattering airborne particle counter for clean spaces, ISO, Geneva
- Whyte, W. and Hejab, M. (2007) Particle and microbial airborne dispersion from people. European Journal of Parenteral and Pharmaceutical Sciences, 12(2): 39-46.
About The Author:
Tim Sandle, Ph.D., is a pharmaceutical professional with wide experience in microbiology and quality assurance. He is the author of more than 30 books relating to pharmaceuticals, healthcare, and life sciences, as well as over 170 peer-reviewed papers and some 500 technical articles. Sandle has presented at over 200 events and he currently works at Bio Products Laboratory Ltd. (BPL), and he is a visiting professor at the University of Manchester and University College London, as well as a consultant to the pharmaceutical industry. Visit his microbiology website at https://www.pharmamicroresources.com.