Is Your Pharma Facility Ready For The Next Public Health Crisis?
By Kelly Cycon, BioSci Consulting
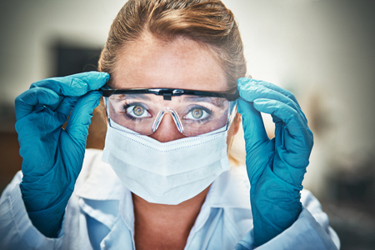
Chances are your biopharma or pharma manufacturing facility is not prepared for the next public health emergency. Sorry, but it's true. We can learn from the past, but preparing thoroughly for what we don't know is practically impossible. It's like TSA preparing for the shoe bomber. For nearly 20 years, we were reminded of that instance every time we boarded a plane, and while precautions are taken at every airport, the unexpected tends to be one step ahead.
Considering recent decisions that have upended public health in our country, it is merely a matter of time before more outbreaks occur. Measles is a current example of this — reduce vaccinations, and vaccine-preventable diseases will naturally reemerge. With travel, any infectious disease can take root in a novel location should an infected passenger engage with others (i.e., Ebola).
This isn't rocket science, but as time passes, people tend to forget how awful something can be, even if they were directly affected by it. Preventive measures wane as a sense of security resumes, which is evident when you consider that the COVID pandemic originated a mere five years ago.
Biopharma and pharmaceutical companies may tick all the boxes when it comes to regulated spaces, but facility architecture and best practices in peripheral areas can play an equally important role in protecting the continuity of work. With previous experience as the director of manufacturing for a laboratory that intentionally grew infectious human viruses, including swine flu/H1N1pdm and SARS-CoV-2, this article focuses on some insights into preparatory activities for when the next infectious disease crisis comes to a place near you.
A little time and effort today can go a long way in helping your business and employees survive, and maybe even thrive. Many lessons were learned from the COVID pandemic, but how many of those lessons are woven into your everyday practices and your emergency preparedness plan? Hopefully, your answer is "some," but here are additional questions, ideas, and activities to prepare your business for the next one.
Practice Good Workplace Hygiene Outside Cleanroom Environments
Every business should have guidelines and a budget to keep its employees safe. Certain daily tasks make sense from a "keep yourself safe from any infectious disease" standpoint. You won’t demean your workforce by reminding them to wash their hands properly with posters in bathrooms and break areas. The majority of pathogenic microbes enter your body through your mouth. Wiping down surfaces before and after lunch is another task that can be easily performed if your business provides a spray bottle of disinfectant or cleaning wipes. Installing and actually refilling sanitizer stations at high-traffic areas within your company is another good practice. Ideally, employees should undergo annual retraining on basic safety measures relevant to their specific roles, as well as general company safety protocols. However, taking personal responsibility for your safety is essential to your health.
Many activities can be built into company-wide SOPs for any emergency — the more automatic a disaster response is, the better. It is why practice drills are performed — to ensure a proper response that requires little thought, just deliberate action. Who determines your company’s level of preparedness? Consider addressing any relevant activities that aren’t in place with your boss, human resources, or the appropriate responsible party.
Design Facilities And Protocols With Employee Safety In Mind
Social distancing, combined with remote and hybrid work arrangements, is crucial for reducing the number of people in the office and maintaining a safe environment. However, this can be a challenge for manufacturing companies where employees are vital to productivity. Consider what percentage of your workforce needs to be on-site to perform their job. How did you manage employee distancing for meetings, lunch breaks, and other activities during COVID? Consider what your policies were like before and after the COVID pandemic. What worked, and what could your company do better? If your company is newer and you lack such policies, don’t delay in starting the discussion to get protocols in place. You’ll thank yourself later.
Include Rigorous Safeguards In Visitor Policies
Your employees may or may not interact directly with customers. Still, chances are you will have visitors come to your door, particularly for outsourced maintenance and repair. Some key questions about how your manufacturing site handles visitors:
- Do you have a plan in place for visitors to enter your facility safely and securely?
- Do you have a sign-in log, disposable PPE, and are they chaperoned while on-site?
- Does an employee interact with couriers who drop off and pick up daily shipments?
- Can any activities be converted to contactless?
- What if a visitor interacts with an employee who reports being ill the next day?
- Is there a method to capture information about and communicate with those who have been in your facility?
Relevant circumstances, decisions, guidelines, and actions should be outlined in a visitor policy.
Map Clear Steps For When An Employee Gets Sick
It is management’s responsibility to ensure employees understand how to maintain their safety and health, as well as what to do in an incident.
Key questions:
- What are the current steps when an employee is suddenly out of work due to illness for more than a day or two?
- Who will take over their role while they are recovering or in quarantine?
- Who did they work with, sit with, or meet with before they got sick?
- Who is responsible for sanitizing the workstation of the sick employee?
- When can the employee return to work?
- How do other employees monitor their health on a daily basis?
During COVID, many places required temperature checks. Chances are, there will be instances you haven't prepared for, but having guidelines in place and clear communication is essential. A lack of preparation and guidance can lead to fear and uncertainty; therefore, do your best as a company to address this. Return-to-work options can change as an outbreak progresses, so have a designee stay informed of current regulations in your state that apply to your company.
Use Cross-Training To Build Morale And Protect Workflows
Do you have contingency plans in place if a significant number of your employees are unable to report to the office? Does your company invest in cross-training its employees? Granted, this isn't a "one size fits most" task, since there are variable levels of education and knowledge.
However, imagine you are suddenly without 30% of your workforce. How will your basic operations continue? Most people are trainable to perform tasks with instruction and guidance, and enjoy being empowered to learn new things. Being a dependable human being is a valuable skill.
Consider scheduling a lunch meeting with your team to gather ideas for cross-training. Encourage creative thinking and pass out tickets for ideas and questions, then draw for prizes. Or create a task bulletin board with employee names and pushpins for the tasks each person has mastered. Training your staff to implement additional skills can boost engagement, morale, and productivity. It can also be built into your promotion and compensation matrix, if you have one.
Get creative in thinking about how to encourage employee participation in the big picture of working as a team. Reflect on the collective input from both employee and individual growth perspectives to benefit cross-training exercises for the company and each employee.
Design Open And Functional Team Communication Channels
When employees are not properly informed about important topics, they come up with answers that tend to be fear-based.
Each employee should know if phone calls, texts, emails, or in-person discussions are adequate. Knowing the criteria for not reporting to work when ill should be posted, then revised as needed over time. How state laws and the number of covered sick days are handled is also something to stay on top of, especially if your company has locations in multiple states.
Define PPE Reuse Parameters For Times Of Short Supply
If you use PPE regularly, do employees use it once and discard it, or do they reuse it? If they reuse the PPE or it becomes short in supply, do you have a sterilization method in place to ensure safe reusability? While day-to-day operations may include “use once and discard” parameters for gloves and face masks, you may permit the reuse of disposable lab coats or Tyvek jumpsuits. What changes can be implemented when stocks are low and PPE is critical to employee safety or manufacturing cleanliness?
Have a strategy for what is acceptable for reuse, what remains use-once-and-discard, and what activities can be performed safely without PPE during a supply chain crisis.
Decide What To Stockpile And Lock In With Backup Vendors
Validation of multiple suppliers for critical materials is a must, whenever possible. Stockpiling makes sense when the materials have a long shelf life or do not expire; otherwise, it can be a gamble.
Key questions:
- Do you have the budget and space to purchase extra inventory of specific items to ensure critical supplies don't run out?
- Are there buffers, solutions, or reagents you can prepare in-house instead of buying pre-made stocks?
- Is there a functional substitute for a material from another manufacturer that you have not yet tested and validated for use?
This can also apply to tubes, pipette tips, and other consumables necessary for your operations.
- Are there any materials that can be manufactured in-house using 3D printing?
- If you invest in producing 3D-printed parts, is there a business case for selling them to other businesses?
Perhaps you are already evaluating other vendors due to tariffs or other sourcing complications. Not all “replacement” materials are created equally. You may be using a cheaper supplier now, but for a few pennies more, you might improve production, quality, or safety. Perhaps a higher-priced reagent made in the U.S. turns out to save you money by working better or lasting longer.
Consider how glove materials (i.e., latex, nitrile) and quality vary widely and correlate with the price per case. Have you ever ripped a glove just trying to put it on? You may use twice as many low-cost gloves compared with a better-quality version that requires only one pair to complete each task.
The aspects of PPE such as permeability, waterproof coating, and thickness can vary for purpose, safety, and comfort. Items that come into contact with the face, such as goggles and face masks, should be used by only one employee and cleaned, sterilized, or discarded between uses. Cheaper, reused face masks can get fuzzy, itchy, and uncomfortable. Reusable PPE should always be labeled with the employee's initials, the date, and perhaps a tally of usage.
Ensure that purchasing power exists for more than one vendor for critical materials, or you will be scrambling for supplies alongside the masses and paying a higher price, not just monetarily.
If your company’s work is vital to addressing or combating a crisis, communicating this to suppliers may increase your purchasing priority among the greater efforts to keep public health workflows functioning.
Assess Space For Social Distancing
Is there space in your business for employees to spread out? Can you install barriers between desks or operational activities? Can you relocate certain activities to a less populated area, or are you at maximum capacity? Thinking through how your space is used and how efficient your systems are can help address any space constraints ahead of time. Spaghetti diagrams and workflow charts can facilitate creative decisions to reduce space requirements for certain activities. Having instruments or special equipment on another floor can increase employee traffic in areas that could be condensed with smaller instruments or more efficient placement for your employees. Setting up picnic tables outdoors for breaks and lunches can also reduce crowding. What options do you have within your company to ensure employee safety and functionality of your business processes?
Prepare For Surge Capacity Or Shutdown
When the next disease outbreak impacts your business, you’ll want to respond, not react. Communicate the company’s expectations to your employees so they understand what could happen. They may have implementable, effective ideas if you empower them with open dialogue.
Key questions:
- Is your business one that thrives in the face of a public health emergency, or did your business temporarily close or barely scrape by during COVID?
- Are you a newer business that hasn’t considered what will happen when the next epidemic hits?
- What is your plan to ensure you and your employees are well-equipped for the challenges?
- How can you ensure continued operation with a minimally viable number of healthy workers?
- What activities must never stop to keep your business open?
- Can you add or repurpose products or services to benefit public health in a time of crisis?
These questions are better thought out when there is time to think and share ideas.
If Nothing Else, Pay Attention To These Takeaways
Effective communication and defined process parameters can go a long way during a public health crisis, but ultimately, no one can prepare for everything that could arise. Planning, discussion, compassion, and leadership are imperative, along with fair and consistent decision-making. As a business, from start-up to corporation, you have responsibilities beyond being profitable.
Key questions:
- Look at your business like a living thing — what does it need to survive and to thrive in the face of adversity?
- What role does your company play in the greater picture of public health?
- What decisions can your company execute now to ensure continued success?
- Are there activities you can bring on-site for internal control, rather than outsourcing them?
- As a thought leader, are there any testing strategies or expertise that could be brought in to ensure a seamless workflow transition under pressure?
- Could you empower current employees to get specialized certifications or training to perform other critical tasks?
- As an employee, what skills can you learn or enhance to better prepare yourself, your coworkers, and the company for the next disaster?
- How can you make yourself indispensable to the company during the next epidemic?
Overall, the take-home message is: What activities make sense for your company and yourself as an employee and as an individual to be prepared for potential emergencies that lie ahead? Many of the suggestions outlined are interdependent and rely on one another for optimal effectiveness. Creative thinking, open discussion, and preparation are the keys to effective execution in response to any emergency.
About The Author:
Kelly A. Cycon, Ph.D., is an independent consultant and principal of BioSci Consulting. Previously, she was a vice president at iFyber, and before that virology director at ZeptoMetrix. She received a Ph.D. in immunology from the University at Buffalo. Connect with her on LinkedIn.