Developing Cell Therapy Packaging And Labeling Is A Time Critical Activity
By Patricia Kessler, owner, PKG Consulting, LLC
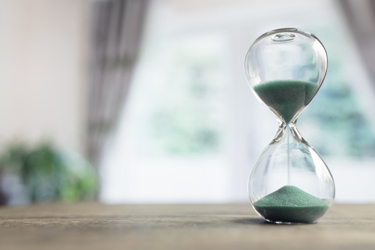
Cell and gene therapy product approvals are on a steep rise. As of May 2020, there are seventeen approved products in the United States, with recent approvals including Kymriah®, Yescarta®, and Zolgensma®.1 The American Society of Gene & Cell Therapy website lists 490 trials under the modalities of cell therapy and gene therapy in the United States alone2. Many of these therapies will need to be stored and shipped at the vapor phase of liquid nitrogen at temperatures between -135°C to -195°C (LN2 temperatures).
Supply chain and regulatory personnel familiar with drug product packaging have likely experienced the scramble of getting packaging layouts and text into regulatory filings, getting quality agreements with packaging and transport service providers in place, and completing packaging qualification protocols at the last minute. When drug approval timelines are abbreviated, the frantic packaging rush is only intensified. Zolgensma®, for example, received Fast-Track, Breakthrough Therapy, Priority Review and Orphan Drug designations.3 These designations can help speed up the regulatory review process considerably, often leading to approval a mere six months after filing. Zolgesma® and Kymriah ®both had five-month approval timelines and Yescarta® had a seven-month approval versus the normal one-year approval timeframe for standard drugs.3, 4, 5 Companies in these situations face extreme pressure to have a marketable product by the expedited approval date. Having qualified packaging in place well before filing will ensure that these launch dates can be met and patients in need of treatment can be helped without delay upon approval.
How else do cell-therapy products differ from standard drugs and biologics?
- Extreme temperature fluctuations: Cell therapy products are exposed to extreme temperature fluctuations from -190°C to 37°C during production, storage, shipping and end use (see Table 1 below) and may have strict time out of labeled storage temperature limitations. Product stability needs to include an assessment of the product at all temperatures expected throughout production and the supply chain and product packaging needs to be designed to withstand these temperatures.
- Labeling requirements: Labeling text requirements for cell therapy often require patient-specific chain of identity and chain of custody labeling, unique NDC codes for various dosing kits, and additional labeling text statements all of which impact label size and placement. Adding in country-specific requirements in multiple languages can also challenge development of product labeling.
- Cost: Finally, cell therapy products are extraordinarily expensive, ranging from thousands to hundreds of thousands of dollars a dose6. As such, it’s imperative that the packaging and distribution system fully protect and represent the high value of cell therapy pharmaceuticals.
Table 1 Example Temperature Map for Cell Therapy Product Stored and Shipped at Vapor Phase of Liquid Nitrogen
How do these differences impact product packaging?
Primary Package Labels
Challenges begin with primary package labeling. Product may need to be frozen within a certain timeframe after formulation and filling which means that cryo-stable bags and vials (see Photos 1 and 2, below) will need to be labeled quickly without normal label cure time needed for the label to adhere properly to the primary package. Label stock and adhesive must be chosen prudently to ensure that labels remain adhered even with a short cure time before being frozen. There are a limited number of label stocks that can handle this type of exposure and even if manufacturer specs claim that a label can be used for frozen applications the label may not work for a particular application throughout the supply chain. Labels rated for frozen applications may fail miserably upon actual use testing and label manufacturers will not guarantee product performance for specific uses – it is up to the purchaser to test and qualify the label stock and adhesive. Labeled primary packages should be thoroughly tested at all storage and use conditions, including product transport, to ensure labels remain attached.
Photo 1
Kymriah® Product Bag © 2020 Novartis
Photo 2
AT Closed Vial 6mL © 2020 Aseptic Technologies (Used with Permission).
It's not only the adhesive and label stock that are of concern. Not every package printing method will hold up to LN2 temperatures so companies will also need to carry out print quality testing on pre-printed labels and on-demand thermal transfer printed labels. Tests must include rub tests at frozen and room temperatures using rubs with water and alcohol, as well as any other antiseptic solution expected to be used on or near the product packaging. Specialized coatings and laminates may be required on printed labels to ensure performance. Product bags and vials will be covered with frost upon removal, so it is important to design the label with the greatest amount of contrast between print and background color (see Photo 2, above).
Most printed label suppliers will not have the ability to carry out testing of products at LN2 temperatures or even at -80°C and since there are no standard tests for frozen label testing, companies will need to develop protocols for use with their specific applications. Final material selection and testing should occur during Phase 3 studies to allow enough time for material selection and testing in preparation for regulatory filing.
Secondary Packaging
Secondary packaging including cartons and metal cassettes are needed to protect frozen bags and vials during transport. Bags are typically shipped in metal cassettes but no standard exists for shipment and storage of LN2 frozen vials. Secondary packs must fit into specific racking systems used in cell therapy LN2 shipping containers and longer-term LN2 storage tanks. LN2 shipping containers vary by supplier and may have different neck diameters and payload volumes (see Photos 3 and 4, below). Supply chain and marketing staff will need to determine the exact end-user requirements for packaging to ensure product can be transferred easily from LN2 shipping container to onsite storage when necessary. LN2 shipping dewars and onsite storage units may have different racking systems and payload limitations.
Photo 3 Cryoport Large Volume Shipper Photo 4 Cryoport EXP 6 Shipper
Packaging must fit within cylindrical chamber and/or inside a metal rack or lifter.
© 2020 Cryoport, Inc. (Used with Permission)
End-users will be wearing protective gloves, so packaging must be designed with the limitations of gloved hands in mind. Handling products at LN2 temperatures is extremely uncomfortable and the process is often rushed, so every effort should be made to simplify the packaging process. In some cases, packaging will need take place in an LN2 temperature controlled cart, known as a CryoCart (see Photos 5 and 6 below). A CryoCart can maintain LN2 temperatures and provide a means to package at LN2 temperatures and move materials between two LN2 storage tanks or from tank to LN2 shipping container. If finished drug product will be stored at an intermediate LN2 warehouse, packaging must be designed to fit specific storage racks (see Photo 6, below).
Photo 5
Photo 5 Chart Industries, Inc. MVE CryoCart
© 2020 Chart Industries Inc. (Used with Permission)
Photo 6
Photo 6 Transferring frozen material from MVE CryoCart to LN2 storage.
© 2020 Core Cryolab, Inc. (Used with Permission)
Despite the abundance of cell therapy products in the pipeline, few products are approved currently; as such, staff at infusion centers and hospitals may not be familiar with handling requirements. Infusion center and hospital customer onboarding should include specific training on LN2 product handling requirements. Test runs of the complete process should be carried out to ensure product can safely and easily be transferred and time-out-of labeled storage temperature can be minimized, ensuring product quality and safety.
If secondary packaging involves a printed folding carton, tests must be carried out on this proposed packaging at anticipated packaging, transport, and use temperatures. Carton glues need to be tested to ensure performance at LN2 temperatures. Paperboard can become stiff and brittle, so care must be taken to design packaging that can withstand folding and insertion into metal racks. Printed graphics should also be tested for performance at low temperatures since cartons can be scratched, bent or dented during shipment and these defects can be exacerbated at frozen temperatures.
Secondary packaging may include plastic boxes, trays and films. Plastics can warp, shrink and crack at ultra-low temperatures while foam products can become brittle and crumble, so any materials intended for use at LN2 temperatures need to be tested throughout the entire supply chain.
If the cell therapy product is intended to be packaged or sold as a kit, be aware that any ancillary items (vial adapters, tubing, syringes, etc.) may not withstand LN2 temperatures and will have to be shipped separately or placed into the top compartment of an LN2 shipper, possibly contained in a pouch or bag, as shown in the photo below.
Photo 6 Interior of Cryoport Large Volume Shipper
© 2020 Cryoport, Inc. Used with Permission
Commercial secondary package development should be started at the beginning of Phase 3 trials to ensure adequate time for testing and refinement of packaging.
Tertiary Packaging
Options available for shipping at LN2 temperatures are increasing and more compact and maneuverable options are being developed (see Photos 3, 4, and 6 above). Shipper choice will be dependent upon payload, duration of shipment, tracking methods required, and customization of interior racking. Understanding the end-user requirements will lead to the best choice of LN2 shipping container. A key consideration is whether the drug will be used immediately, kept in the dewar for a few days, or transferred to long term LN2 storage. The choice of LN2 shipping container will also impact air transport options and routes as not all containers will fit onto narrow body aircraft, which now make up a majority of passenger flights and an increasing percent of cargo flights.7
Labeling Text
Development of labeling text is an often overlooked task during regulatory filing preparation. The frenetic rush can be avoided if this process is started earlier, preferably before the middle of Phase 3 trials. A text generation and approval procedure should be in place and agreed upon by Regulatory Affairs, Quality Assurance, Supply Chain, Package Development, Marketing and Legal. Roles and responsibilities should be clear and reviewers and approvers should have experience in product labeling. Ideally, the text should be reviewed and approved separately from and before the package design is initiated to avoid costly package design revisions. Labeling should be discussed with FDA as soon as possible in the pre-submission process.
Cell therapy labeling needs to adhere to both drug and biologics labeling guidelines and may need to comply with additional labeling requirements for human tissue products. The concentration of the product may need to be identified by noting a range of cells, minimum number of cells, or target number of cells. It is crucial to obtain feedback from all impacted departments and FDA and other regulatory bodies before deciding on how the concentration will be identified. Be prepared for several rounds of review and negotiation during the FDA review process and make sure the package design will accommodate the addition or deletion of text and/or graphics.
Ultimately, packaging and labeling for cell therapy products needs to be developed early on given the potential for shortened approval timelines and the complexity of manufacturing and distribution at harsh LN2 temperatures. Packaging should be tested using protocols that fully represent the intended packaging, distribution, and end-user processes. Time-out-of-temperature limits should be established to accommodate the range of temperatures encountered during the process. By preparing early and finalizing packaging before regulatory applications are filed, cell therapy companies can ensure their products will be ready to ship immediately upon approval, providing life-saving drugs to patients as quickly as possible.
---
References
1 U.S Food & Drug Administration “Approved Cellular and Gene Therapy Products” https://www.fda.gov/vaccines-blood-biologics/cellular-gene-therapy-products/approved-cellular-and-gene-therapy-products
2 The American Society of Gene & Cell Therapy’s Clinical Trials Finder
https://app.emergingmed.com/asgct/home
3 U.S. FDA Zolgensma® (onasemnogene abeparvovec-xioi) Summary Basis for Regulatory Action May 24, 2019 https://www.fda.gov/media/127961/download
4 U.S. FDA Kymriah® (tisagenlecleucel) Summary Basis for Regulatory Action August 30, 2017 https://www.fda.gov/media/107962/download
5 U.S. FDA Yescarta® (axicabtagene ciloleucel) Summary Basis for Regulatory Action October 19, 2017 https://www.fda.gov/media/108788/download
6 Cade Hildreth, “Pricing of Approved Cell Therapy Products – Stem Cells, CAR-T, And More,” BioInformant, 22 October 2018, Web 05 June 2020. https://bioinformant.com/price-of-cell-therapy-products/
7 Doug Cameron, “Airlines Turn Away from Big Jets,” Wall Street Journal Online 18 November 2019, Web 05 June 2020 https://www.wsj.com/articles/airlines-turn-away-from-big-jets-11573992001
Photos used with permission from Aseptic Technologies, Chart Industries, Inc., Core Cryolab Inc, and Cryoport, Inc.
About the Author:
Patricia Kessler is the owner of PKG Consulting, LLC, which specializes in cell and gene therapy labeling and packaging. She has more than twenty five years of experience in U.S. and international packaging, labeling, supply chain, and operations in large and small biotech, cell therapy, and gene therapy companies. Patricia worked as a consultant at Kite Pharma during the launch of Yescarta® and is currently working with other cell and gene therapy companies on packaging, labeling and product launch planning. She has a BS in Packaging Science from Rochester Institute of Technology, Rochester NY. You can reach her on LinkedIn: linkedin.com/in/patricia-kessler-73108a17